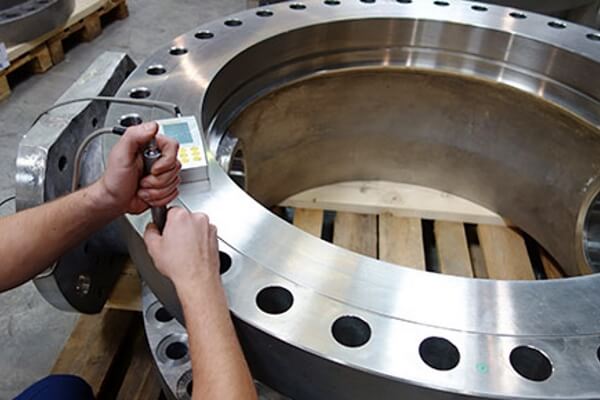
The starting signal of the ultrasounds (starting echo) and the one reflected from the surface opposite to the entrance one (bottom echo), are displayed on the instrument screen with peaks, whose distance is proportional to the time that the ultrasounds take for travel the round trip from the probe to the reflective surface inside the material. If during this path the ultrasonic beam encounters discontinuities, they act as reflectors, and on the screen, between the two previous peaks, others will appear which represent indications relative to the type of discontinuities encountered.
The ultrasonic control lends itself to measuring the thicknesses (thickness) of industrial products, such as tanks, pipes or boilers.